Zinc-Nickel
Zinc-nickel, ZnNi for short, is an electrolytic, inorganic, corrosion-protecting coating system for components in extremely corrosive environments.
It provides significantly better corrosion protection than zinc alone.
The zinc layer is alloyed with 12–15% nickel in the layer.
Zn/Ni meets the nickel emissions requirements according to SS-EN 1811.
Our plants that offer this process:
- Forsheda
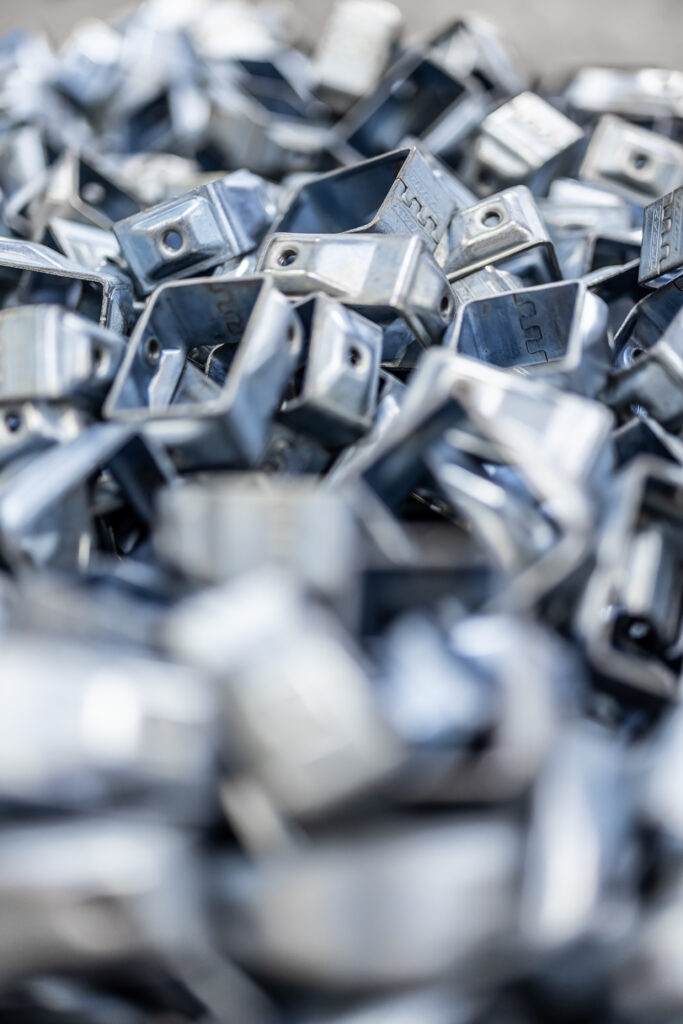
Do you know that our passivations are cobalt-free?
We work for a more sustainable future, by choosing a cobalt-free alternative we make a positive difference both for people and environment.
Why Zinc-Nickel?
The thickness of the coating can be adapted to customer requirements, but provides extremely good corrosion-protecting properties even with thin coatings, >5 μm.
This coating does not create galvanic corrosion in aluminium joints.
It has a low potential difference, which relates to the amount of energy required to move an electrical charge from one point to another.
The application temperature range is <+300°C
Abrasion resistance is hardness 450HV.
If you need friction control, this can be attained with a sealer/topcoat.
Which products are suitable for Zinc-Nickel?
Applications placed in an extremely corrosive environment such as:
- Bolted joints
- Fasteners
- Fittings
- Pipes
- Sheet metal structures
Applied by hanging or drum application.
Which requirements does Zinc-Nickel comply with?
- Complies with VOLVO STD 121-0003 Y1000-4, 121-0004 Y2000-4, 121-0006 Y400-4, 121-0013 Y1300-4, 121-0015 Y1500-4
- Complies with Scania 4111-B(C)3-IF.
- Complies with the ELV and RoHS directives.
> 720 hrs to base material corrosion according to ISO 9227 (NSS).
A sealer provides increased corrosion protection.
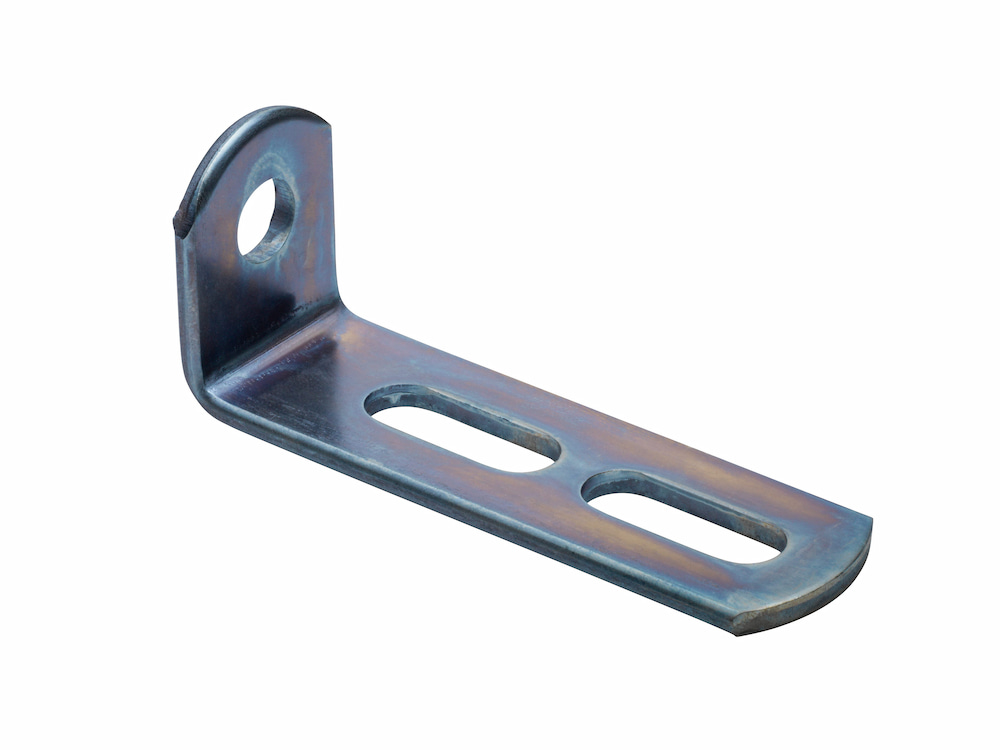
Iridescent blue finish
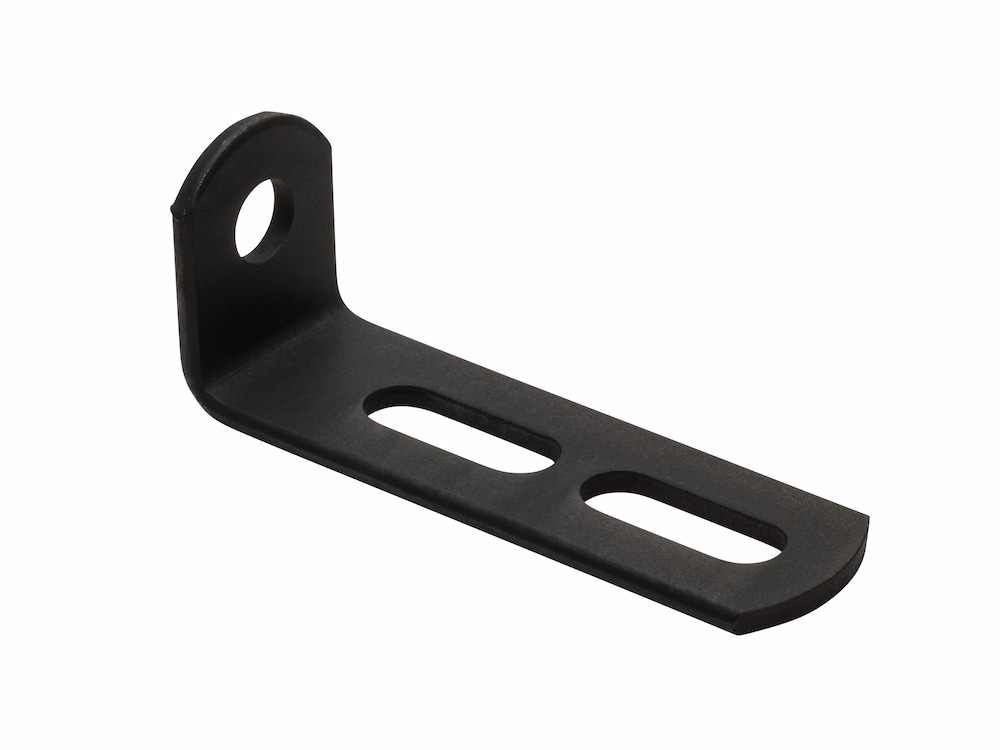
Iridescent satin black finish
Want to know more?
Welcome to contact us to ask your questions and discuss which surface treatment meets your requirements and preferences.