Next steps to climate neutrality
Proton Finishing is the Proton Group’s pioneer in climate calculations. In the winter of 2021, the first climate calculation was completed at Proton Finishing in Forsheda. Since 2023, all Proton Finishing companies offer climate calculations.
– “In addition to knowing in black and white where to take action, we can now give our customers detailed information about how the surface treatment they choose affects the climate,” says process developer and team leader Joel Pierre.
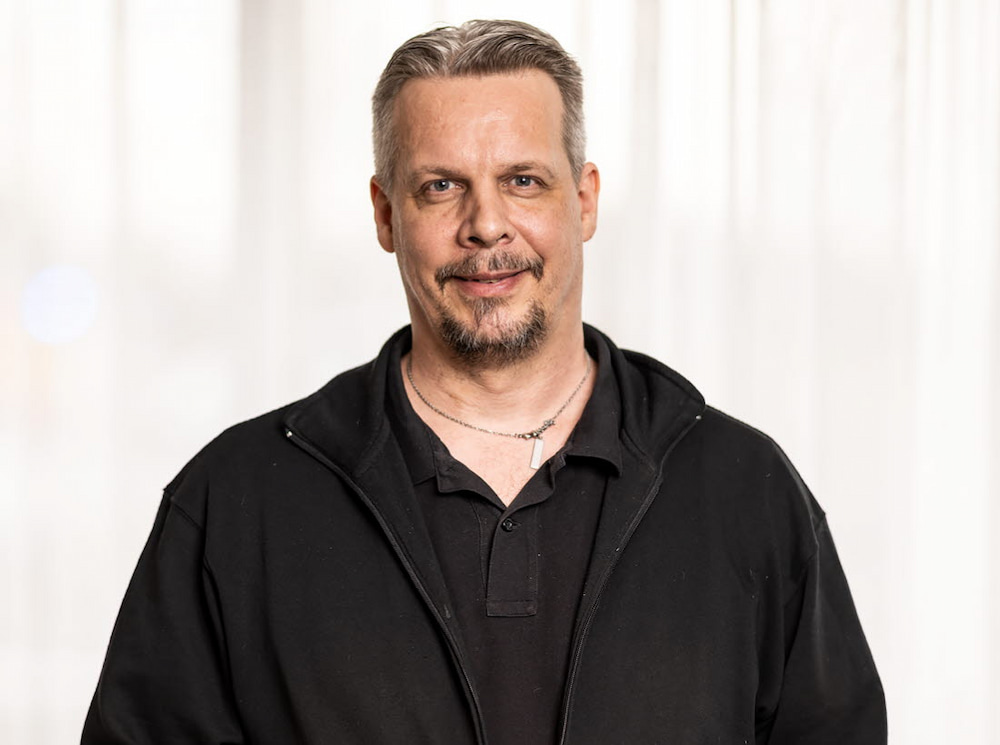
Joel Pierre is a process developer and team leader for Proton Finishing’s development department.
Joel Pierre works as a process developer and team leader at Proton Finishing. His mission is to improve Proton Finishing’s work in the work environment, environment and energy and to run various development projects, including the company’s climate calculations. In the winter of 2021, work began on producing climate calculations for all of Proton Finishing’s units. At the beginning of 2023, all GHG protocols were ready and are used by customers in their sustainability reporting, for Proton Finishing’s own improvement work and are also included in quotations.
What is a climate calculation?
– We calculate our carbon footprint by converting all the climate impacts of our operations into CO2 equivalents*. These calculations cover all our processes both upstream and downstream of the plant. They also take into account energy sources and the CO2 emissions of products before they reach us, as well as the climate impact of our waste.
* Conversion of the impact of all greenhouse gases, expressed in a converted common unit.
Sounds complex?
– It is. The tricky thing is that climate calculations are fairly new to everyone, there is not much to go on. But now that climate calculations have been made for all companies in Proton Finishing, we have set a structure that works and that we can continue to work from, for other businesses in Proton Group. What we have learned is that a close dialogue with our suppliers is required; the purchase of chemicals and energy constitutes a large part of the climate impact for us. Many of our suppliers have not had this information but have produced it at our request. And that takes some time and patience. By making these demands on our suppliers, we are also helping to drive development. Several of our customers have also started to make the same demands on us.
How do you deal with the carbon footprint questions you receive from customers?
– We use the climate calculations to produce key figures per surface treated and line. This means that the customer not only gets to know the average for the entire plant, but can get detailed information about what differentiates the various processes and base their decisions on this. It’s great to be able to provide customers with climate calculations at the quotation stage, and sometimes even earlier, which customers appreciate.
What do the climate projections show now that everyone is ready?
– The use of LPG is a huge culprit, although we knew that before, we may not have realised what proportion it actually accounts for. But powders and zinc balls are also heavy items, partly because they are the main products but they also have the highest emission factors, so this is something we will continue to work on. We have already changed the supplier of zinc balls and made climate benefits through that change.
Do you have any other projects in the pipeline?
– Because LPG is such a large part of our climate impact, we are looking at alternative solutions, such as electric boilers and district heating. We also have several energy efficiency projects underway at the moment, for example, we have installed electricity meters and heat meters on all lines where we
can plan and control the electricity load and heat consumption in a smarter way and thus reduce energy consumption. We are also working on a project where we can reuse the heat from our curing ovens to heat the process and since powder coating requires a lot of energy, we are also testing low-curing powders where we hope that we will be able to cure the powder at a lower temperature to save energy.
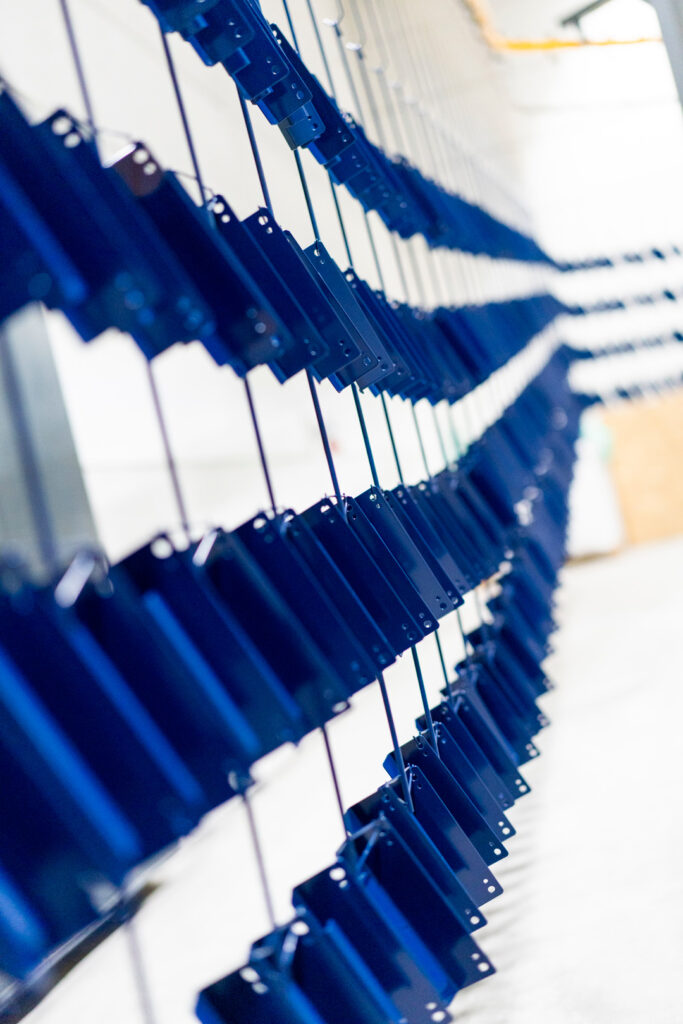
Surface treatment is in some cases an energy-intensive process.
Want to know more?
You are welcome to contact us to ask your questions and discuss which surface treatment fulfils your requirements and wishes.